Hercules Input Devices Driver
Introduction
- Hercules Input Devices Driver
- Hercules Dj Driver Download
- Hercules Input Devices Driver Vga
- Hercules 4 Mx Driver
Hercules 6V-36V, 16Amp Motor Driver can take up to 30A peak current load and can be operated up to 3 KHz PWM. Motor driver can be interfaced with 3.3V and 5V logic levels. Motor driver has built-in protection from under / over voltage, over temperature and short. The Motor driver has terminal block as power connector and 7 pin 2510 type relimate connector for the logic connection. It is suitable for high performance robots, Robocon, Robo-cup, US First, Battle robots etc.

Note:
Video Input Device. Drivers & Utilities. Discuss: Hercules WebCam Deluxe - web camera Series Sign in to comment. Be respectful, keep it civil and stay on topic. Guillemot Hercules Hercules 16/12 FW Driver for Windows 2000/XP 32-bit and Mac OS X 10.3.0. DJ Phatso PRO Infinity Hercules Support Team Member since 2005 VDJ works best in ASIO with the RMX when configured this way: Inputs: None Ouputs: Headphones (Master: Chan 1&2 / Headphones: Chan 3&4) Sound card: DJ Console RMX Check the box 'Apply EQ on Input' (which will make VDJ use the ASIO driver of the Rmx). Download Hercules DJ Console ASIO DJ Control Air Windows Drivers Device: Any device Bios Cameras Game Devices Input Devices Laptops - Desktops Modems Motherboards Network Adapters Other Printers Projectors Scanners Sound Cards USB Video Adapters. Download for free Realtek Input6.3.9600.3 microphone Driver for Windows 10 (x64).
Hercules 6V-36V, 16Amp Motor Driver can take up to 20Amp current if fan is installed on top of heat sink.
Specifications
Hercules Input Devices Driver
- Operating voltage: 6V to 36V
- Continuous output current: 16Amp
- Peak output current: 30Amps
- Maximum PWM Frequency: 3 KHz
- Over voltage and under voltage shutdown
- Thermal shutdown
- Protection against loss of GND and Vcc.
- Motor fault diagnostics outputs for over temperature or short circuit
- Power Connector: 4 Pin Terminal Block
- Logic Connector: 7 pin female relimate connector (2510 type)
- Size: 72.0mm x 38.0mm
Hercules Dj Driver Download
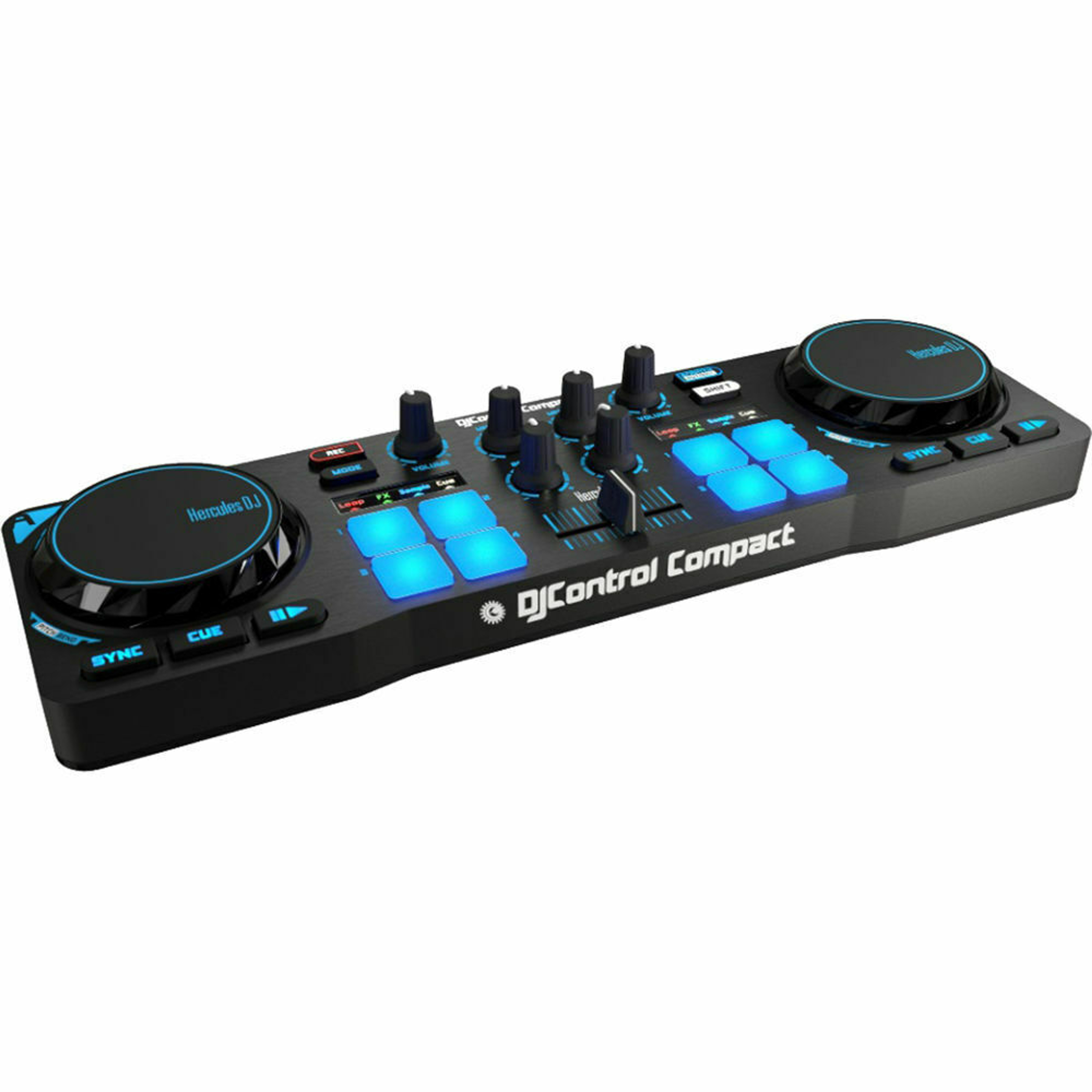
Hercules Input Devices Driver Vga
Package contains
15cm,7 pin female 2510 type relimate connectorFour 10mm mounting studs
Eight M3 mounting screw
Hercules 4 Mx Driver
Important
- Use multithread copper wire with at least 1.5mm2 area of cross section for proper current handling capacity.
- It is highly recommended to use of 15A or 20A fuse in between motor driver’s supply line.
- Motor driver is not reverse polarity protected. Applying reverse polarity will instantly damage the motor driver.
- Make sure that motor supply ground and logic ground is common.
- If you change motor’s direction suddenly while motor is moving in one direction even at 4Amps, depending on the type of the motor, surge current may reach to very high value and motor driver may go in to protection mode. Do not reverse the motor’s direction suddenly unless its required. It’s a good practice to give stop command to the motor for 10 to 100 milliseconds between sudden direction changes.
Correct Motor Driver Selection
For generic motion control applications we recommend Hercules series motor driver that provides satisfactory performance at affordable price. However, for precision servo control applications, Super Hercules series motor driver is strongly recommended. Following is the difference between these two series of the motor drivers.

In case of the Hercules series Motor Drivers, the PWM OFF signal switch off the lower MOSFETs. Which means during PWM off period the motor is free wheeling. DC brakeing is achieved by connecting IN-1 and IN-2 to the logic 1 or logic 0 simultaneously.
Super Hercules series Motor Drivers actually shorts the motor winding during PWM off cycle for tight motion control. It also uses Synchronous Rectification to reduce power dissipation across MOSFETs when motor windings are shorted. In order to do all this, it uses high power MOSFETs and smart motion control methods. In this case, DC brakeing is achieved by simply setting PWM to logic low.
Interfacing motor driver with the microcontroller
To drive the motor controller you just need PWM, INA and INB pins. These pins can have 5V as well as 3.3V logic levels. Diagnostics 1 (DG-1) and Diagnostics-2 (DG-2) pins are internally pulled up at 5V at the motor driver side and are only required if you want to detect over temperature and short circuit faults. Most of the microcontrollers which operate at 3.3V have 5V tolerant input pins. If pins are not 5V tolerant then to interface them to 3.3V logic level you need to scale down 5V to 3.3V logic using open collector buffers or any other 5V to 3.3V logic converters.
Use Fuse Holder with Fuse Blow Indicator to protect motor driver from overload
Recommended Motors Super Hercules DC Motor with Planetary Gearbox and Side Shaft Super Heavy Duty DC Gear Motors | |
Recommended Battery Any High discharge 3cell 11.1V Lithium Polymer battery above 1800mAh. |
Connections
Motor Connector Pins
Pin | Functionality |
Ground | Ground pin to be connected to the supply |
Vcc | Motor supply 6V to 36V DC |
OUT-1 (A) | Output 1 for the motor |
OUT-2 (B) | Output 2 for the motor |
Logic input Connections:
Pin No. | Pin | Functionality |
1 | ENA | Ground |
2 | IN-1 | Logic input for the motor direction. |
3 | Diagnostic 1 (DG-1) | Output pin with logic 1 output in normal operation. Represents side of the internal H bridge corresponding to IN-1. Pin is pulled to logic low by the motor driver in case of over temperature or overload due to short circuit. |
4 | PWM | Used to apply Pulse Width Modulation to control motor velocity |
5 | Diagnostic 2 (DG-2) | Output pin with logic 1 output in normal operation. Represents side of the internal H bridge corresponding to IN-2. Pin is pulled to logic low by the motor driver in case of over temperature or overload due to short circuit. |
6 | IN-2 | Logic input for the motor direction.. |
7 | CS | No Connection |
If you want to drive motor without using PWM then connect PWM pin to 5V logic level
Truth Table in Normal Operating Conditions
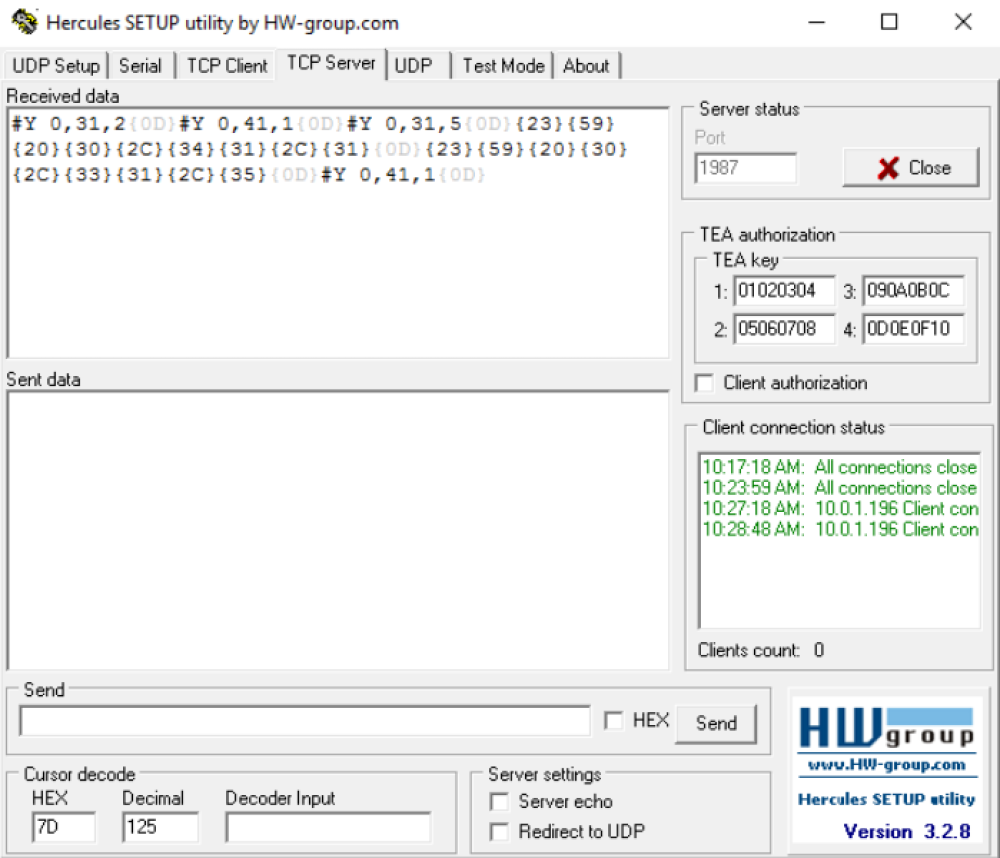
IN-1 | IN-2 | Diagnostic 1 (DG-1) | Diagnostic 2 (DG-2) | OUT-1 (A) | OUT-2 (B) | CS | Mode of Operation |
1 | 1 | 1 | 1 | H | H | N.A. | Break to VCC |
1 | 0 | 1 | 1 | H | L | N.A | Clockwise(CW) |
0 | 1 | 1 | 1 | L | H | N.A | Counterclockwise (CCW) |
0 | 0 | 1 | 1 | L | L | N.A. | Break to GND |
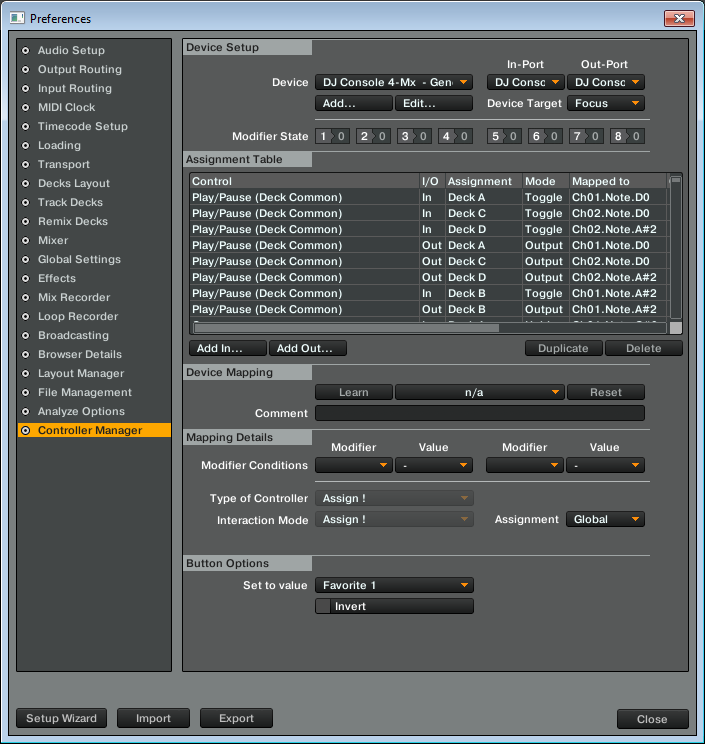
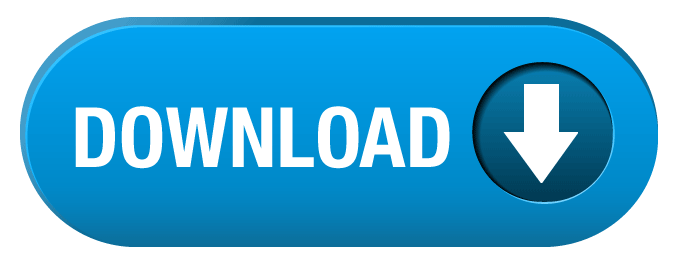